Stainless Steel 6.4 Units
.In, stainless steel, also known as inox steel or inox from French inoxydable , is a, with a minimum of 10.5% content and a maximum of 1.2% by mass.Stainless steels are most notable for their, which increases with increasing chromium content. Additions of increase corrosion resistance in reducing acids and against pitting attack in chloride solutions. Thus, there are numerous grades of stainless steel with varying chromium and molybdenum contents to suit the environment the alloy must endure. Stainless steel's resistance to corrosion and staining, low maintenance, and familiar luster make it an ideal material for many applications where both the strength of steel and corrosion resistance are required.Stainless steels are rolled into, plates, bars, wire, and tubing to be used in:,; construction material in large buildings, such as the; industrial equipment (for example, in, ); and storage tanks and tankers for chemicals and food products (for example, and ). Stainless steel's corrosion resistance, the ease with which it can be steam cleaned and sterilized, and no need for surface coatings has also influenced its use in and food processing plants. Stainless steel (bottom row) resists better than (top row) or alloys (middle row)Stainless steels do not suffer uniform corrosion, like carbon steel, when exposed to wet environments. Unprotected carbon steel readily when exposed to the combination of air and moisture.
Stainless Steel 6.4 is a modification of Medieval II: Total War Download the mod here: http://www.twcenter.net/forums/showthread.php?417435-Stainless-Steel-6.
The resulting surface layer (the rust) is porous and fragile. Since iron oxide occupies a larger volume than the original steel this layer expands and tends to flake and fall away exposing the underlying steel to further attack.
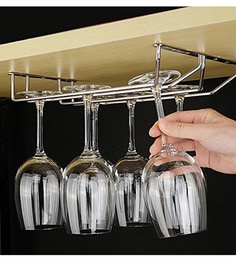
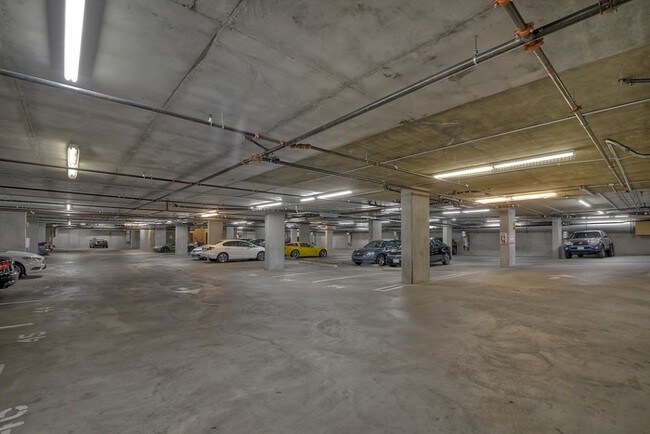
In comparison, stainless steels contain sufficient chromium to undergo, spontaneously forming a microscopically thin inert surface film of chromium oxide by reaction with the oxygen in air and even the small amount of dissolved oxygen in water. This passive film prevents further corrosion by blocking oxygen diffusion to the steel surface and thus prevents corrosion from spreading into the bulk of the metal. Stainless steel is not completely immune to corrosion as shown in this equipment. Acids Acidic solutions can be put into two general categories: reducing acids, such as hydrochloric acid and dilute sulfuric acid, and, such as nitric acid and concentrated sulfuric acid. Increasing chromium and molybdenum content provides increased resistance to reducing acids, while increasing chromium and silicon content provides increased resistance to oxidizing acids.is one of the largest tonnage industrial chemicals manufactured. At room temperature Type is only resistant to 3% acid while Type is resistant to 3% acid up to 50 °C and 20% acid at room temperature. Thus Type 304 is rarely used in contact with sulfuric acid.
Type and are resistant to sulfuric acid at even higher concentrations above room temperature.Concentrated sulfuric acid possesses oxidizing characteristics like nitric acid and thus silicon bearing stainless steels also find application.will damage any kind of stainless steel, and should be avoided.All types of stainless steel resist attack from and at room temperature. At high concentration and elevated temperature attack will occur and higher alloy stainless steels are required.In general, are less corrosive than mineral acids such as hydrochloric and sulfuric acid. As the molecular weight of organic acids increase their corrosivity decreases. Has the lowest molecular weight and is a weak acid. Type 304 can be used with formic acid though it will tend to discolor the solution. Is probably the most commercially important of the organic acids and Type 316 is commonly used for storing and handling acetic acid. Bases Stainless steels Type and are unaffected by any of the weak bases such as, even in high concentrations and at high temperatures.
The same grades of stainless exposed to stronger bases such as at high concentrations and high temperatures will likely experience some etching and cracking.Increasing chromium and nickel contents provide increasing resistance.Organics All grades resist damage from and, though in the latter case Type is preferable to; will damage 304 unless the temperature is kept low. Fats and only affect Type 304 at temperatures above 150 °C (302 °F), and Type 316 above 260 °C (500 °F), while Type 317 is unaffected at all temperatures.
Type 316L is required for processing of. Localized corrosion Localized corrosion can occur in a number of ways, e.g. Such localized attack is most common in the presence of. Increasing chloride levels require more highly alloyed stainless steels.Localized corrosion can be difficult to predict because it is dependent on many factors including:. Chloride ion concentration (However, even when the chloride solution concentration is known, it is still possible for chloride ions to concentrate, such as in crevices (e.g. Under gaskets) or on surfaces in vapor spaces due to evaporation and condensation.). Increasing temperature increases susceptibility.
Increasing acidity increases susceptibility. Stagnant conditions increase susceptibility. The presence of oxidizing species, such as ferric and cupric ionsPitting corrosion resistance This is probably the most frequent form of corrosion.
The corrosion resistance of stainless steels to pitting corrosion is often expressed by the PREN (Pitting Resistance Equivalent Number) obtained through the formula:PREN =%Cr+3.3%Mo+16%N where the terms correspond to the contents by weight% of Chromium, Molybdenum and Nitrogen respectively in the steel.The higher the PREN, the higher the pitting corrosion resistance. Increasing chromium, molybdenum and nitrogen contents provide increasing resistance to pitting corrosion.Crevice corrosion While the PREN is a property of the stainless steel, crevice corrosion occurs when poor design has created confined areas (overlapping plates, washer-plate interfaces, etc.) and when the PREN is not high enough for the service conditions. Design and good fabrication techniques combined with correct alloy selection can prevent such corrosion. Left is not stainless and isLike steel, stainless steels are relatively poor conductors of electricity, with significantly lower than copper.and stainless steels are.Annealed stainless steels are. Can make austenitic stainless steels slightly magnetic.Galling , sometimes called cold welding, is a form of severe adhesive wear which can occur when two metal surfaces are in relative motion to each other and under heavy pressure.
Austenitic stainless steel fasteners are particularly susceptible to thread galling, although it also occurs in other alloys that self-generate a protective oxide surface film, such as aluminum and titanium. Under high contact-force sliding this oxide can be deformed, broken and removed from parts of the component, exposing bare reactive metal. When the two surfaces are the same material, these exposed surfaces can easily fuse together.
Separation of the two surfaces can result in surface tearing and even complete seizure of metal components or fasteners.Galling can be mitigated by the use of dissimilar materials (bronze against stainless steel), or using different stainless steels ( against ). Additionally, threaded joints may be to provide a film between the two parts and prevent galling. Also, 60, made by selective alloying with manganese, silicon and nitrogen, has demonstrated a reduced tendency to gall.History. An announcement, as it appeared in the 1915 New York Times, of the development of stainless steel in, England.The corrosion resistance of iron-chromium alloys was first recognized in 1821 by French metallurgist, who noted their resistance against attack by some acids and suggested their use in.
Stainless Steel 6.4 Hre Units
Metallurgists of the 19th century were unable to produce the combination of low carbon and high chromium found in most modern stainless steels, and the high-chromium alloys they could produce were too brittle to be practical.In 1872, the Englishmen and patented a 'Water Resistant' alloy in Britain, that would today be considered a stainless steel.: 11In the late 1890s, of Germany developed an aluminothermic process for producing carbon-free chromium. Between 1904 and 1911 several researchers, particularly of France, prepared alloys that would today be considered stainless steel.In 1908, built the 366-ton sailing yacht featuring a chrome-nickel steel hull in Germany. In 1911, reported on the relationship between chromium content and corrosion resistance. On 17 October 1912, engineers Benno Strauss and Eduard Maurer patented stainless steel as.Similar developments were taking place contemporaneously in the United States, where Christian Dantsizen and Frederick Becket were industrializing stainless steel.
In 1912, applied for a US patent on a stainless steel alloy, which was not granted until 1919. Monument to at the former in, EnglandIn 1912, of the research laboratory in, England, while seeking a corrosion-resistant alloy for gun barrels, discovered and subsequently industrialized a martensitic stainless steel alloy. The discovery was announced two years later in a January 1915 newspaper article in.The metal was later marketed under the 'Staybrite' brand by in England and was used for the new entrance canopy for the in in 1929. Brearley applied for a US during 1915 only to find that Haynes had already registered a patent. Brearley and Haynes pooled their funding and with a group of investors formed the American Stainless Steel Corporation, with headquarters in,.In the beginning, stainless steel was sold in the US under different brand names like ' and 'Nirosta steel'.
Even within the metallurgy industry the eventual name remained unsettled; in 1921 one trade journal was calling it 'unstainable steel'. In 1929, before the Great Depression hit, over 25,000 tons of stainless steel were manufactured and sold in the US. Stainless steel families. Main article:There are four main families, which are primarily classified by their: austenitic, ferritic, martensitic and duplex.Austenitic stainless steel is the largest family of stainless steels, making up about two-thirds of all stainless steel production. They possess an austenitic microstructure, which is a crystal structure. This microstructure is achieved by alloying with sufficient nickel and/or manganese and nitrogen to maintain an austenitic microstructure at all temperatures from the region to the melting point.
Thus austenitic stainless steels are not hardenable by heat treatment since they possess the same microstructure at all temperatures.Their is low (200 to 300MPa), which limits their use for structural and other load bearing components. Duplex stanless steels tend to be preferred in such situations because of their high strength and corrosion resistance.Their is high, which allows very important deformation in fabrication processes (such as deep drawing of kitchen sinks)They are weldable by all processes. The most frequently used is electric arc.Thin sheets and small diameter bars can be strengthened by cold working, with an associated reduction of elongation. However, if they are welded, the welded area will return to the low strength level of the steel before cold working.
This limits the use of cold-worked austenitic stainless steels.They are essentially non-magnetic and maintain their ductility at cryogenic temperatures.They can be further subdivided into two sub-groups, 200 series and 300 series:. 200 Series are chromium-manganese-nickel alloys, which maximize the use of manganese and nitrogen to minimize the use of nickel. Due to their nitrogen addition they possess approximately 50% higher yield strength than 300 series stainless steels.
Type 201 is hardenable through cold working; Type 202 is a general purpose stainless steel. Decreasing nickel content and increasing manganese results in weak corrosion resistance.
300 Series are chromium-nickel alloys, which achieve their austenitic microstructure almost exclusively by nickel alloying; some very highly alloyed grades include some nitrogen to reduce nickel requirements. 300 series is the largest group and the most widely used. The best known grade is Type, also known as 18/8 and 18/10 for its composition of 18% chromium and 8%/10% nickel, respectively.
The second most common austenitic stainless steel is Type. The addition of 2% molybdenum provides greater resistance to acids and to localized corrosion caused by chloride ions.Low-carbon versions, for example or 304L, are used to avoid corrosion problems caused by welding. The 'L' means that the carbon content of the alloy is below 0.03%.Ferritic stainless steels Ferritic stainless steels possess a ferrite microstructure like carbon steel, which is a crystal structure, and contain between 10.5% and 27% chromium with very little or no nickel. This microstructure is present at all temperatures, due to the chromium addition, and like austenitic stainless steels these are not hardenable by heat treatment. They cannot be strengthened by cold work to the same degree as austenitic stainless steels. They are magnetic like carbon steel.As they do not contain Nickel, they cost less than austeniticgrades and are now present in a wide range of industries.Common grades are 409 and 409Cb (Cb is the US name for Nb) with about 10;5%Cr, the latter being used mostly for automobile exhaust pipes in North America, 430 (17%Cr) for architectural applications, for kitchenware, sinks, slate hooks, roofing, etc.). Additions of Nb, Ti, Zr to grade 430 allow a good weldability and such grades are used for automotive exhaust pipes, for white goods (dishwashers, refrigerator doors, chimney ducts, solar water heaters etc.Higher Cr ferritics (22%Cr) are now used for power plates for (SOFC) operating at temperatures around 700°C.Electrical resistance ferritic grades Fr-Cr-Al are not included in these groups, as they are designed for oxidation resistance at elevated temperatures.
Martensitic stainless steels Martensitic stainless steels offer a wide range of properties and are used as stainless engineering steels, stainless tool steels, and creep resisting steels. They fall into 4 categories (with some overlap):. Fe-Cr-C grades: They were the first grades used and they are still widely used in engineering and wear-resistant applications.
Fe-Cr-Ni-C grades: In these grades, some of the carbon is replaced by nickel. They offer a higher toughness and a higher corrosion resistance. Grade EN 1.4303 (Casting grade CA6NM) with 13%Cr and 4%Ni is used for most, and in s because it has good casting properties, a good weldability and a good resistance to erosion. Precipitation hardening grades: Grade EN 1.4542 (a.k.a. 17/4PH), the best known grade, combines martensitic hardening and precipitation hardening. It achieves high strength and good toughness and is used in aerospace among other applications.
Creep-resisting grades: Small additions of Nb, V, B, Co increase the strength and creep resistance up to about 650 °C.Heat treatment of martensitic stainless steels form a family of stainless steels that can be heat treated to provide the adequate level of mechanical properties.The heat treatment typically involves three steps:. Austenitizing, in which the steel is heated to a temperature in the range 980 - 1050 °C depending on the grades. The austenite is a face centered cubic phase. Quenching (a rapid cooling in air, oil or water).
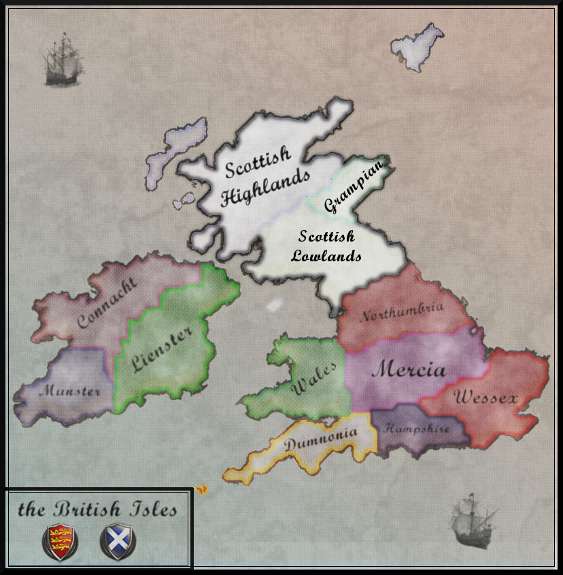
The austenite is transformed into martensite, a hard crystal structure. The as-quenched martensite is very hard and too brittle for most applications. Some residual austenite may remain. Tempering, i.e. Heating to around 500 °C, holding at temperature, then air cooling. Increasing the tempering temperature decreases the and but increases the elongation and the impact resistance.Nitrogen-alloyed martensitic stainless steels Replacing some of the carbon in martensitic stainless steels by nitrogen is a fairly recent development.
The limited solubility of nitrogen has been increased by the (PESR) process in which melting is carried out under a high nitrogen pressure. Up to 0.4% nitrogen contents have been achieved leading to higher hardness/strength and higher corrosion resistance.
As the PESR is expensive, lower but significant nitrogen contents have been achieved using the standard (AOD) process.They are magnetic. They are not as corrosion resistant as the common ferritic and austenitic stainless steels due to their low chromium content.Duplex stainless steel have a mixed microstructure of austenite and ferrite, the aim usually being to produce a 50/50 mix, although in commercial alloys the ratio may be 40/60. They are characterized by high chromium (19–32%) and molybdenum (up to 5%) and lower nickel contents than austenitic stainless steels. Duplex stainless steels have roughly twice the of austenitic stainless steels.
Their mixed microstructure provides improved resistance to chloride stress corrosion cracking in comparison to austenitic stainless steels Types and.Duplex grades usually divieded into three sub-groups based on their corrosion resistance: lean duplex, standard duplex and super duplex.The properties of duplex stainless steels are achieved with an overall lower alloy content than similar-performing super-austenitic grades, making their use cost-effective for many applications.The pulp and paper industry was one of the first ones to use extensively duplex stainless steel. Today, the oil and gas industry is the largest user and has pushed for more corrosion resistant grades, leading to the development of super duplex and even so-called hyper duplex grades. 316L stainless steel, with an unpolished, mill finishStandard can be applied to flat rolled stainless steel directly by the rollers and by mechanical abrasives. Steel is first rolled to size and thickness and then to change the properties of the final material. Any that forms on the surface is removed by, and a passivation layer is created on the surface. A final finish can then be applied to achieve the desired aesthetic appearance.
No. 0: Hot rolled, annealed, thicker plates.
No. 1: Hot rolled, annealed and passivated. No. 2D: Cold rolled, annealed, pickled and passivated. No. 2B: Same as above with additional pass through highly polished rollers.
No. 2BA: Bright annealed (BA or 2R) same as above then bright annealed under oxygen-free atmospheric condition. No. 3: Coarse abrasive finish applied mechanically.
No. 4: Brushed finish. No.
5: Satin finish. No. 6: Matte finish (brushed but smoother than #4).
No. 7: Reflective finish. No. 8: Mirror finish.
No. 9: Bead blast finish. No. 10: Heat colored finish—offering a wide range of and heat colored surfacesProduction process and figures Production process Most of the world stainless steel production is produced by the following processes. EAF (Electric Arc Furnace) in which stainless steel scrap, other ferrous scrap and ferro alloys (Fe Cr,Fe-Ni, Fe Mo, Fe Si.) are melted.
The molten metal is then poured into a ladle and transferred into the AOD. AOD (Argon Oxygen Decarburization) allows the removal of carbon in the molten steel and other composition adjustments to achieve the desired chemical composition of the steel. CC (Continuous Casting) in which the molten metal is solidified into slabs (typical section is 20 cm thick and 2 m wide) for flat products or blooms (sections vary widely but 25cmx25cm is about the average). HR (Hot Rolling): The slabs and blooms are reheated in a furnace and then hot rolled. Hot rolling reduces the thickness of the slabs to produce about 3mm thick coils. Blooms on the other hand are hot rolled into bars (that are cut into lengths at the exit of the rolling mill) or wire rod which is coiled.
CF (Cold finishing): This is a very simplified overview.Hot rolled coils are pickled in acid solutions to remove the oxide scale on the surface, then subsequently cold rolled (Sendzimir rolling mills), annealed in a protective atmosphere, until the desired thickness and surface finish is obtained. Further operations such as slitting, tube forming, etc. Can be carried out in downstream facilities.Hot rolled bars are straightened, then machined to the required tolerance and finish.Wire rod coils are subsequently processed to produce. cold finished bars on drawing benches.
fasteners on boltmaking machines. wire on single or multipass drawing machinesFurther information can be obtained on the websites of most producers. An example is provided here. Production figures World stainless steel production figures re published every year by ISSF.Overall stainless steel production (flat and long products):Stainless steel meltshop production in 1000 metric TonsYear. See also:The worked with on various with stainless steel bodies from the 1930s through the 1970s to demonstrate the material's potential. The 1957 and 1958 Eldorado Brougham had a stainless steel roof. In 1981 and 1982, the production automobile used Type- stainless steel body panels over a.
Intercity buses made by are partially made of stainless steel.The largest use of stainless steel in cars is the exhaust line. Environment protection requirements of reducing pollution and noise for whole life of cars led to the use of ferritic grades typically AISI409/409Cb in North America, EN 1.4511 and 1.4512 in Europe. They are used for collector, tubing, muffler, catalytic converter, tailpipe. Heat resisting grades typically EN1.4913 or 1.4923 are used in parts of turbochargers, other heat resisting grades for EGR and for inlet and exhaust valves. In addition, common rail injection systems and particularly the injectors rely on stainless steels.Stainless steel has proved to be the best choice for miscellaneous applications, such as stiffeners for windshiel wiper blades, balls for seat belt operation device in case of accident, springs, fasteners, etc.The aft body panel of the model (2-door coupe hatchback) is made of stainless steel. It was discovered during early body prototyping that conventional steel could not be formed without cracking (due to the many curves and angles in that automobile). Thus, was forced to use stainless steel on the Cayman.Some use stainless steel as decorative highlights in their vehicles.Passenger rail carsRail cars have commonly been manufactured using corrugated stainless steel panels (for additional structural strength).
This was particularly popular during the 1960s and 1970s, but has since declined. One notable example was the early. Notable former manufacturers of stainless steel rolling stock included the (USA), which has been licensed to Japan's, and the Portuguese company. Many railcars in the United States are still manufactured with stainless steel. India is developing its rail infrastructure and has started to put new stainless steel coaches in service. South Africa is also commissioning stainless steel coaches.
AircraftBudd also built two airplanes, the and the, of stainless steel tube and sheet. The first, which had fabric wing coverings, is on display at the, being the longest continuous display of an aircraft ever, since 1934. The Was almost all stainless steel, save for the control surfaces. One survives at the, adjacent to.The American of 1936 was also built using a spot-welded stainless steel hull.Due to its thermal stability, the Bristol Aeroplane Company built the all-stainless steel high-speed research aircraft, which first flew in 1963. However, the practical problems encountered meant that employed aluminium alloys.Similarly the experimental mach 3 American bomber, the, made extensive use of stainless steel in its external structure due to the extreme heat encountered at those high speeds.The use of stainless steel in mainstream aircraft is hindered by its excessive weight compared to other materials, such as.Spacecraft. Further information:Surgical tools and medical equipment are usually made of stainless steel, because of its durability and ability to be sterilized in an.
In addition, such as bone reinforcements and replacements (e.g. Hip sockets and cranial plates) are made with special alloys formulated to resist corrosion, mechanical wear, and biological reactions. Stainless steel is used in a variety of applications in dentistry. It is common to use stainless steel in many instruments that need to be sterilized, such as needles, endodontic files in, metal posts in root canal–treated teeth, temporary crowns and crowns for, and arch wires and brackets in orthodontics. The surgical stainless steel alloys (e.g., low-carbon steel) have also been used in some of the early dental implants.
Energy Stainless steels are extensively used in all manner of power stations, from nuclear to solar.
Finishing TouchesOnce the installation comes to an end you will be presented with a choice:Choose whatever takes your fancy, you can change this setting at a later stage before starting a campaign by running the ‘Run Setup’ short cut from the Stainless Steels short cut menu.Next you will be presented with this option screen, again choose what you want, you can change it later. Choosing one of the AI options is mandatory. Once you click 'OK' your choices get implemented which may take a little while depending on the items selected. Steam specific StuffThe installer now displays the message underneath, you can safely ignore the suggestion regarding the non steam game link, the desktop short cut provided by the installer works just fine:The set upinstallation will now attempt to start the mod, but if you are new to mod installations for Steam andor have never done the copyrename of the executable then you will be presented with this error message:Unfortunately, the launcher does not use www.twcenter.net, it only detects that the kingdoms.exe required to run the disk version is not present.
This can easily be fixed by following my tutorial here:Once you have run that tutorial simply rundouble click the Stainless Steel desktop shortcut to start the mod, it is however recommended to install 6.4 first. The original installation of Stainless Steel does not provide STRING.BIN files (which the game references) as these are generated automatically at game start from the TXT files in the datatext folder.
Unfortunately, the Steam version of the game does not generate these files from the battle, shared, strat and tooltips TXT files.Included in the www.twcenter.net in PDF form is a folder called ‘text’ that contains these missing files and their original TXT counterpart – simply extract the folder into the modsSS6.3data folder and allow overwriting of existing files. There is an unofficial fix available which does a good job in reducing errors. It's called Meloo's Bugfix and is www.twcenter.net. Please read the instructions carefully, especially if you apply the patch at a later stage.I made an www.twcenter.net from it which also fixes the text issues (BIN files not generated by Steam). Again, make sure to read the instrucitons in the www.twcenter.net.www.twcenter.net has a www.twcenter.net where you can post queries regarding problems with the mod.